To control the quality of spot welding 3 parameters are taken into consideration : welding current value, time of the welding impulse and welding force, which is defined by the pressure force value and deviation of the force between electrodes. While welding current and time can be easily measured and controlled directly, force is usually managed by indirect indicators what leads to deviations in actual force values when operating conditions change.
For example, in most conventional cells, the welding force is controlled based on the actuator motor current value. This approach does not take into account the processes occurring during the operation of the welding cell - a change in temperature and the state of the grease, a change in the motor torque as a result of the closing distance change after tips dressing, the wear of gearbox parts, wear of the weld gun mechanisms. All the factors cause a deviation of the actual welding force from the set one. In a long run such deviations above the allowable limits lead to welding defects.
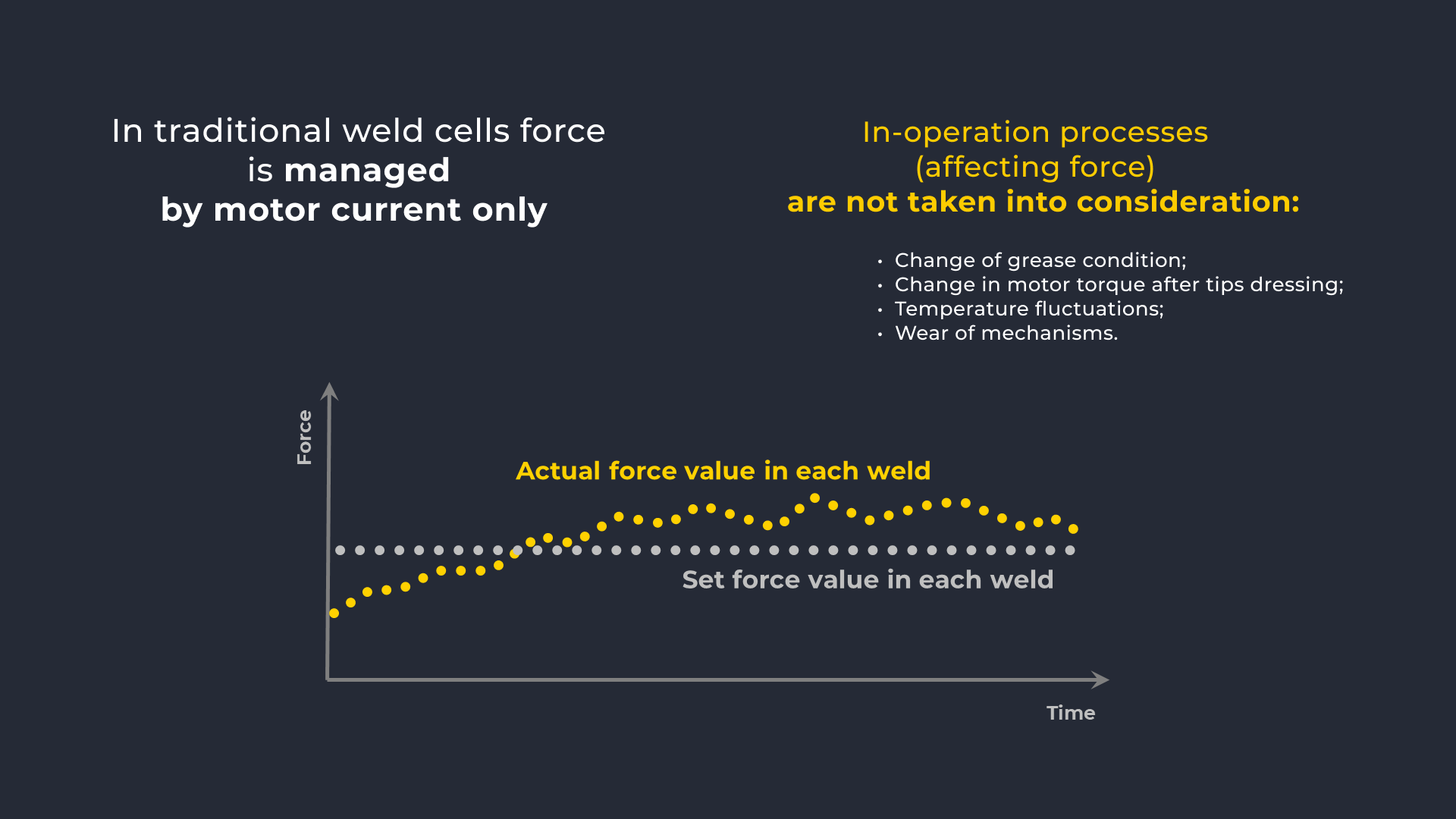
The difference in force values between the electrodes is also not reliably measured, while deviations in the position and thickness of the welded parts lead to uneven actual forces at electrodes, which negatively affects the quality of welding
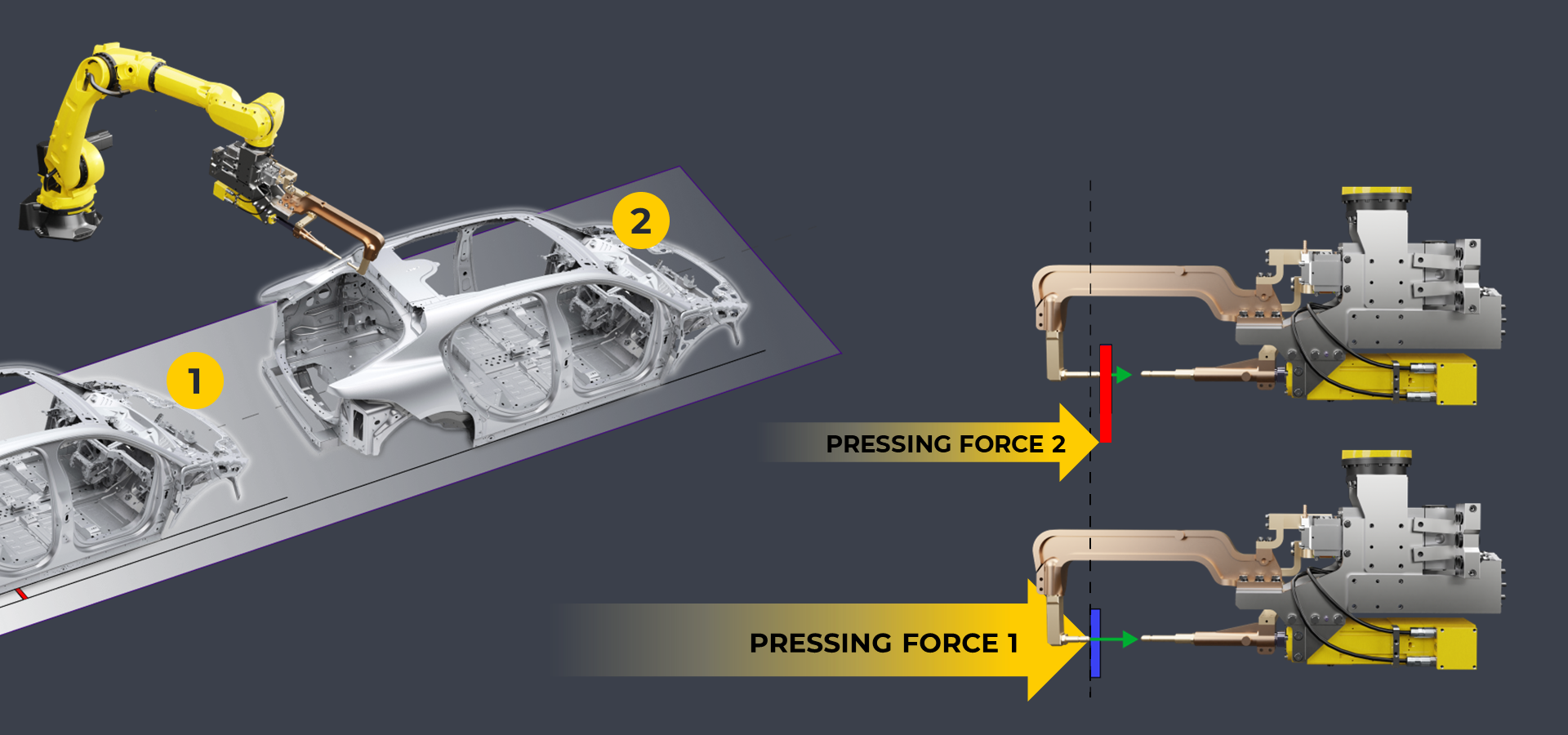
The weld gun electrode actuator is traditionally controlled by the robot controller. The time to reach the maximum speed of all drives is usually limited by the general settings of the robot and defined for large robot mechanism and moving parts.. The limitation justified for the inertial masses of the robot is redundant for a significantly less inertia of the weld gun motor and does not allow reaching the minimum opening and closing time of the gun that the actuator is capable of.
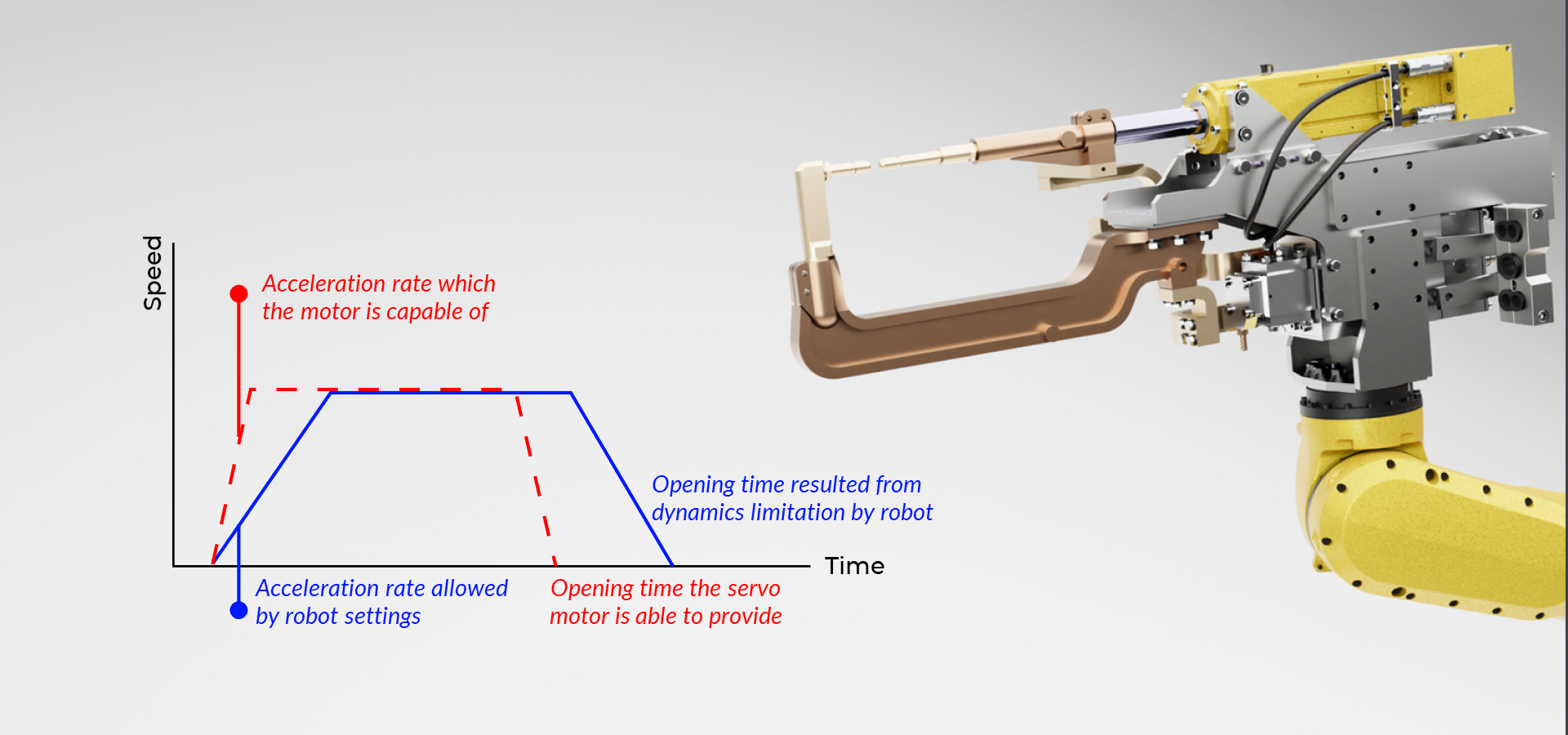
The weld gun electrode actuator is traditionally controlled by the robot controller. The time to reach the maximum speed of all drives is usually limited by the general settings of the robot and defined for large robot mechanism and moving parts.. The limitation justified for the inertial masses of the robot is redundant for a significantly less inertia of the weld gun motor and does not allow reaching the minimum opening and closing time of the gun that the actuator is capable of.
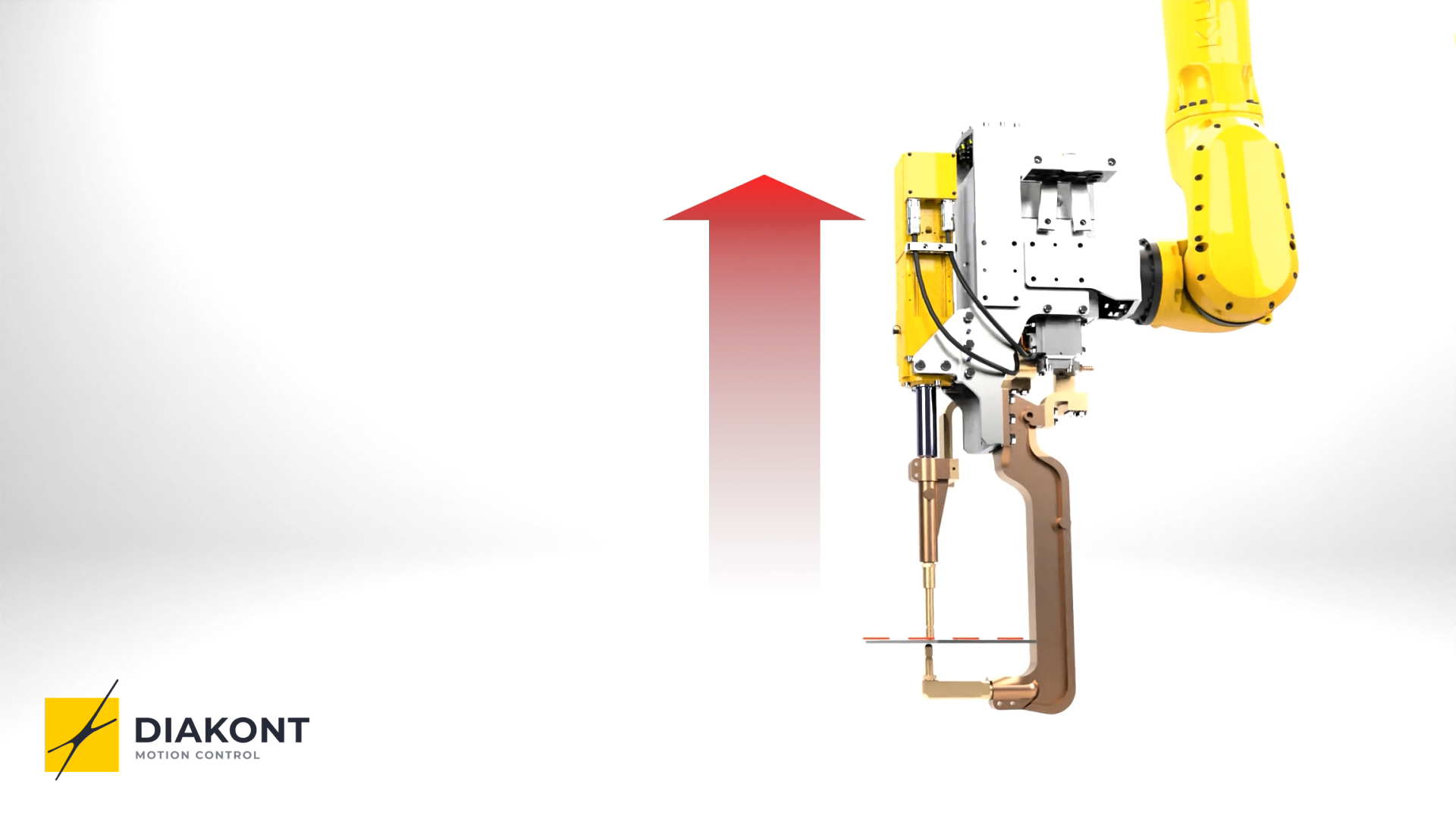
After welding to move to the next point the weld gun electrodes are retracted from the part. The fixed electrode is retracted by moving the weld gun by the robot. Due to the need for retraction, the trajectory and time of movement of the welding gun between weld spots is increased. A robot has to retract the gun from the part and then move to the next point by optimal path. To reduce the travel time the retraction distance is usually. minimized, but this increases the risk of damaging the surface of the welded part due to sticking of the electrodes after welding.
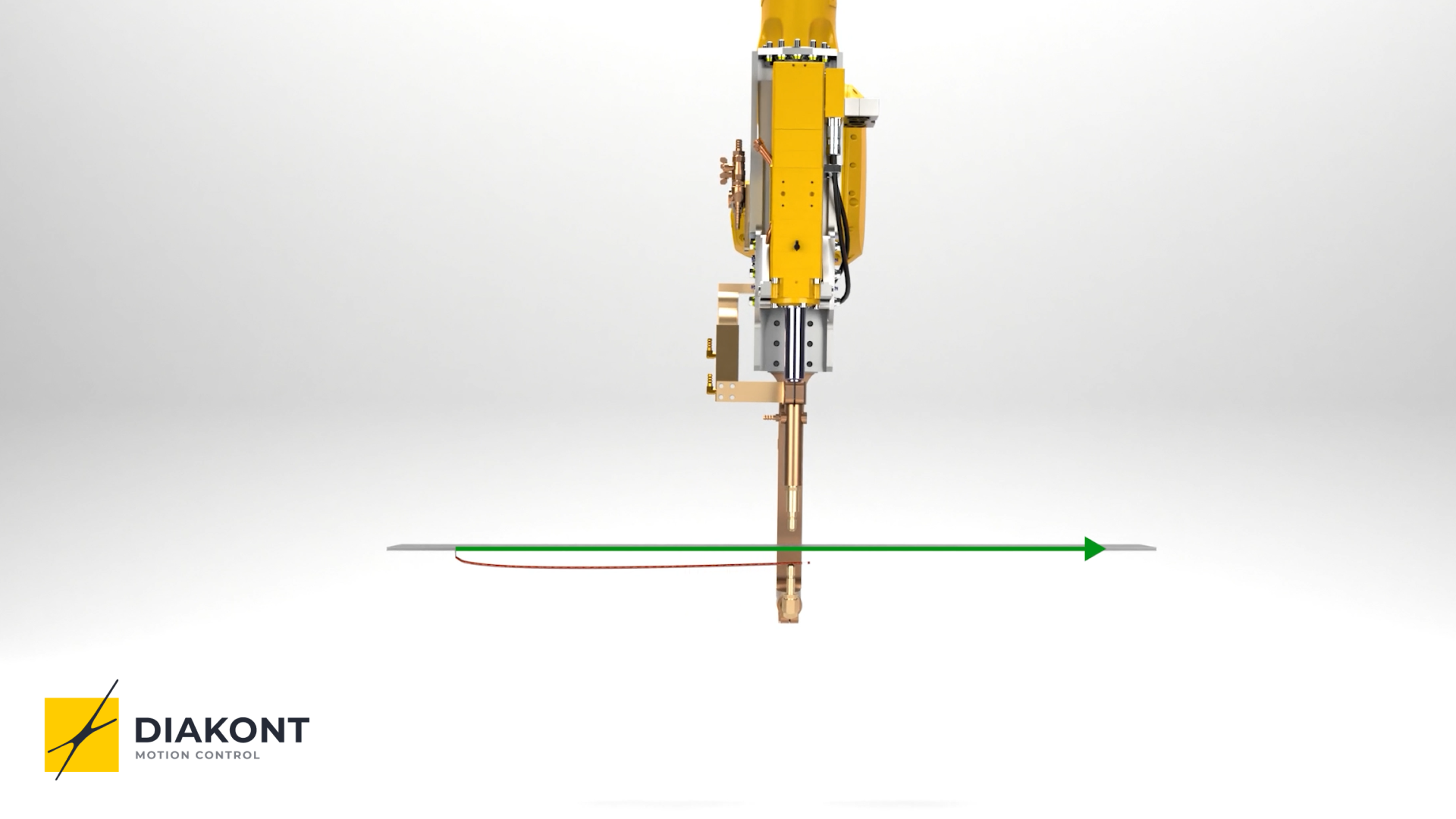
When preparing a welding program. each cell system undergoes a separate adjustment procedure: weld gun motion trajectory is programmed, force cyclogram and weld gun opening parameters are set, and parameters for sharpening/replacing electrodes are tuned. Overall, a setting of many parameters in several separate systems, as well as configuring their interaction is required. This takes a lot of time and places high requirements on the qualifications of the staff.
During the line operation to maintain correct welding forces a periodic calibration of the force of the weld guns is carried out. Calibration is usually carried out at least once a quarter and takes additional time from the service personnel.